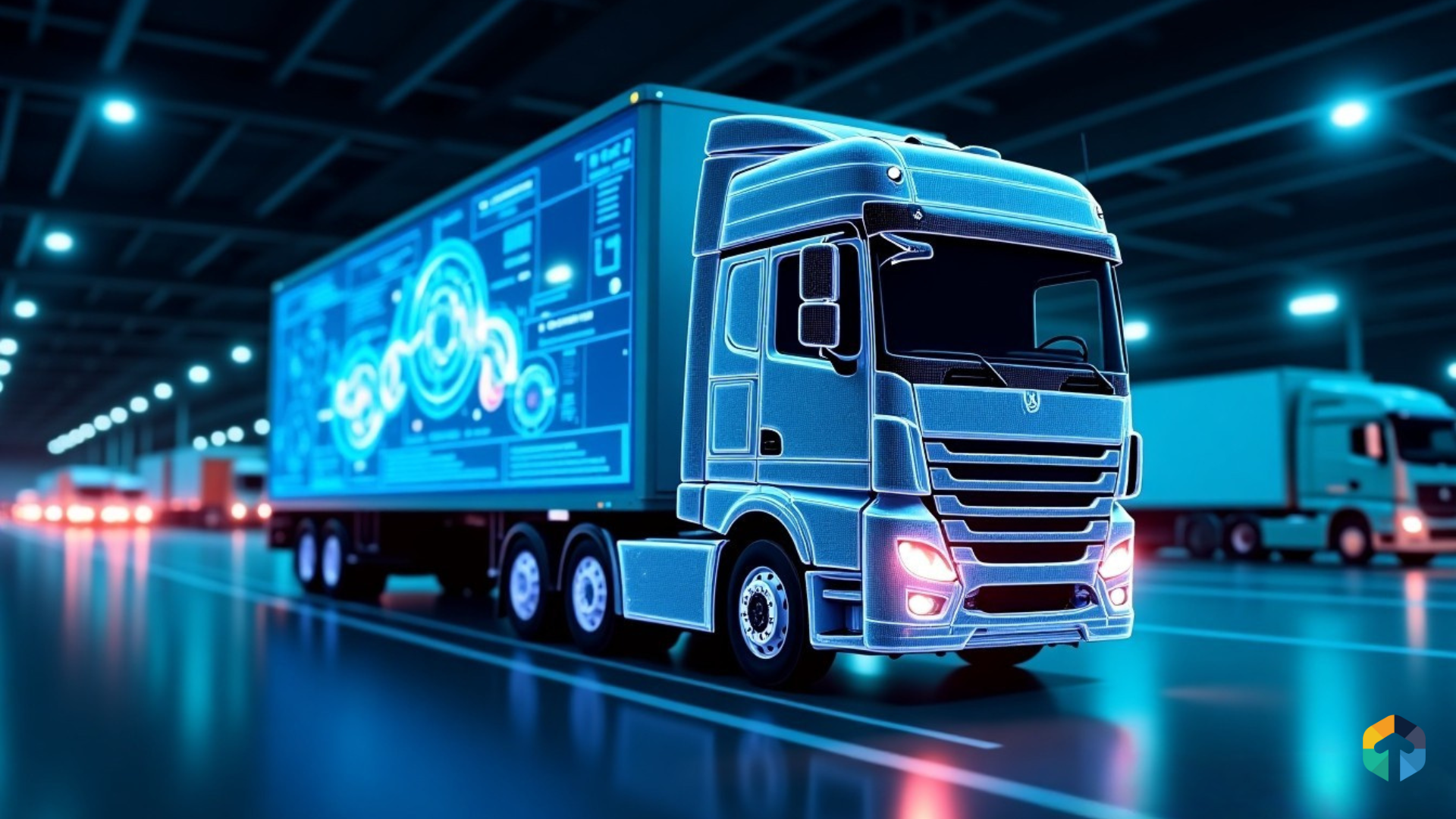
The Daily Challenge of Vehicle Inspection Compliance
Every day across America, commercial drivers spend valuable time completing mandatory vehicle inspection reports, often using outdated paper forms or clunky digital interfaces.
Table of Contents
Transportation safety managers frequently note that drivers spend substantial time daily on inspection paperwork, time they could otherwise use for moving freight or rest periods.
This inspection bottleneck creates multiple problems: drivers rush through important safety checks, fleet managers receive inconsistent data, and compliance officers struggle to maintain proper documentation.
Industry research indicates that paperwork inefficiencies cost trucking companies thousands of dollars per driver annually, with inspection reporting representing a significant portion of this burden.
Understanding AI Inspection Reporting
AI agents for vehicle inspection reporting represent a practical solution to this industry-wide challenge.
Rather than forcing drivers to navigate complex forms, these systems use conversational interfaces to guide inspection processes through natural dialogue.
The technology combines voice recognition, natural language processing, and industry-specific knowledge to transform what was once a tedious documentation exercise into a straightforward conversation.
This approach maintains compliance requirements while dramatically improving the driver experience.
Transportation companies implementing similar solutions have documented significant reductions in inspection completion time while improving data accuracy.
Safety directors often comment that these tools aren't just about efficiency, they're about getting better safety data because drivers aren't rushing through the process.
Key Features That Improve Driver Reporting
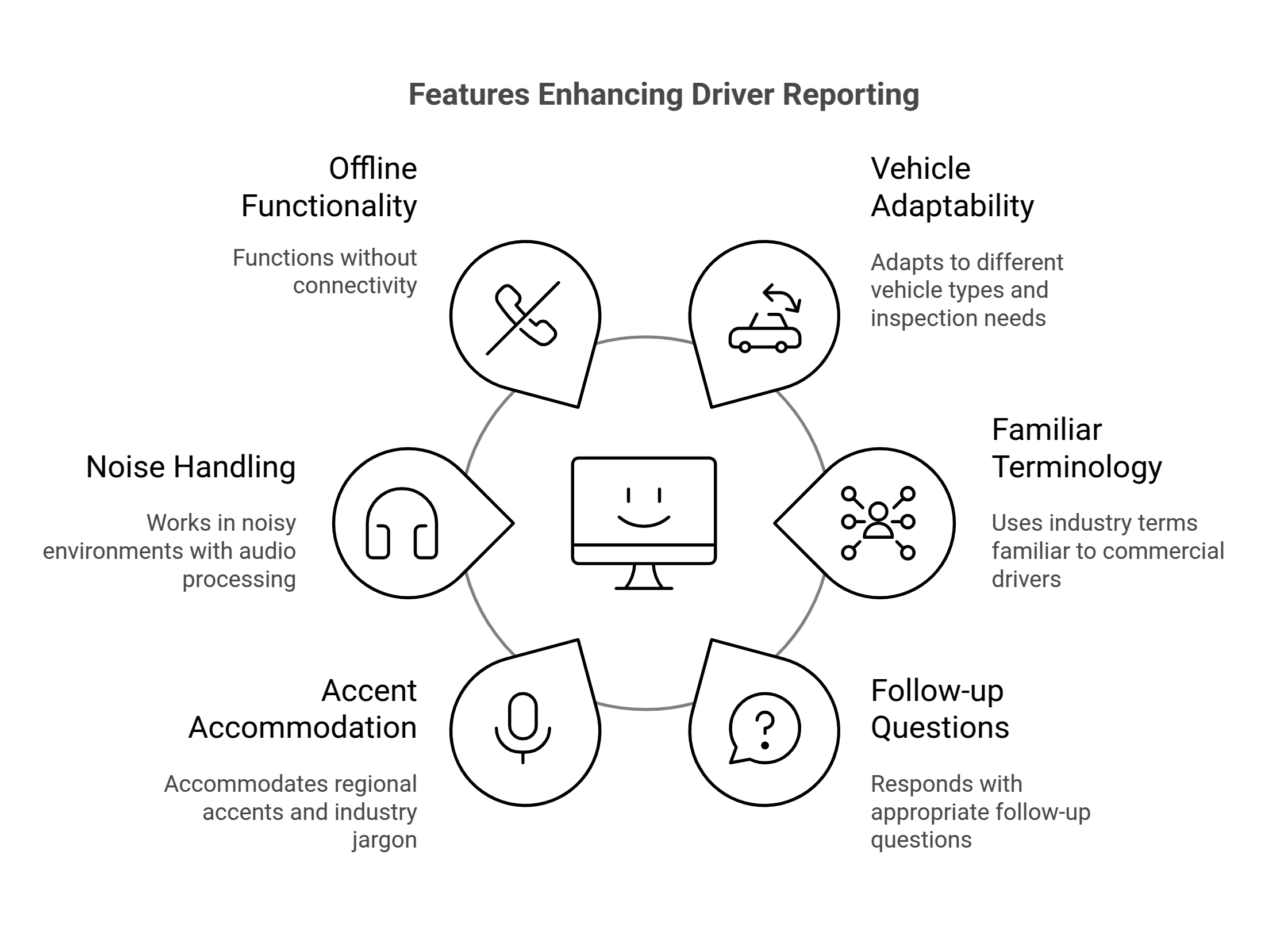
Conversational Interface That Speaks the Driver's Language
Instead of navigating complicated forms, drivers interact with an AI agent that guides them through inspections using natural conversation. The system
Adapts to different vehicle types and inspection requirements.
Uses industry terminology familiar to commercial drivers.
Responds to verbal responses with appropriate follow-up questions.
Accommodates regional accents and industry jargon.
Works in noisy environments through specialized audio processing.
Functions offline when connectivity is unavailable.
Delivery companies find that most drivers prefer this approach over traditional reporting methods.
Experienced drivers often describe it as having a knowledgeable colleague helping through the inspection rather than fighting with paperwork.
Intelligent Data Capture and System Integration
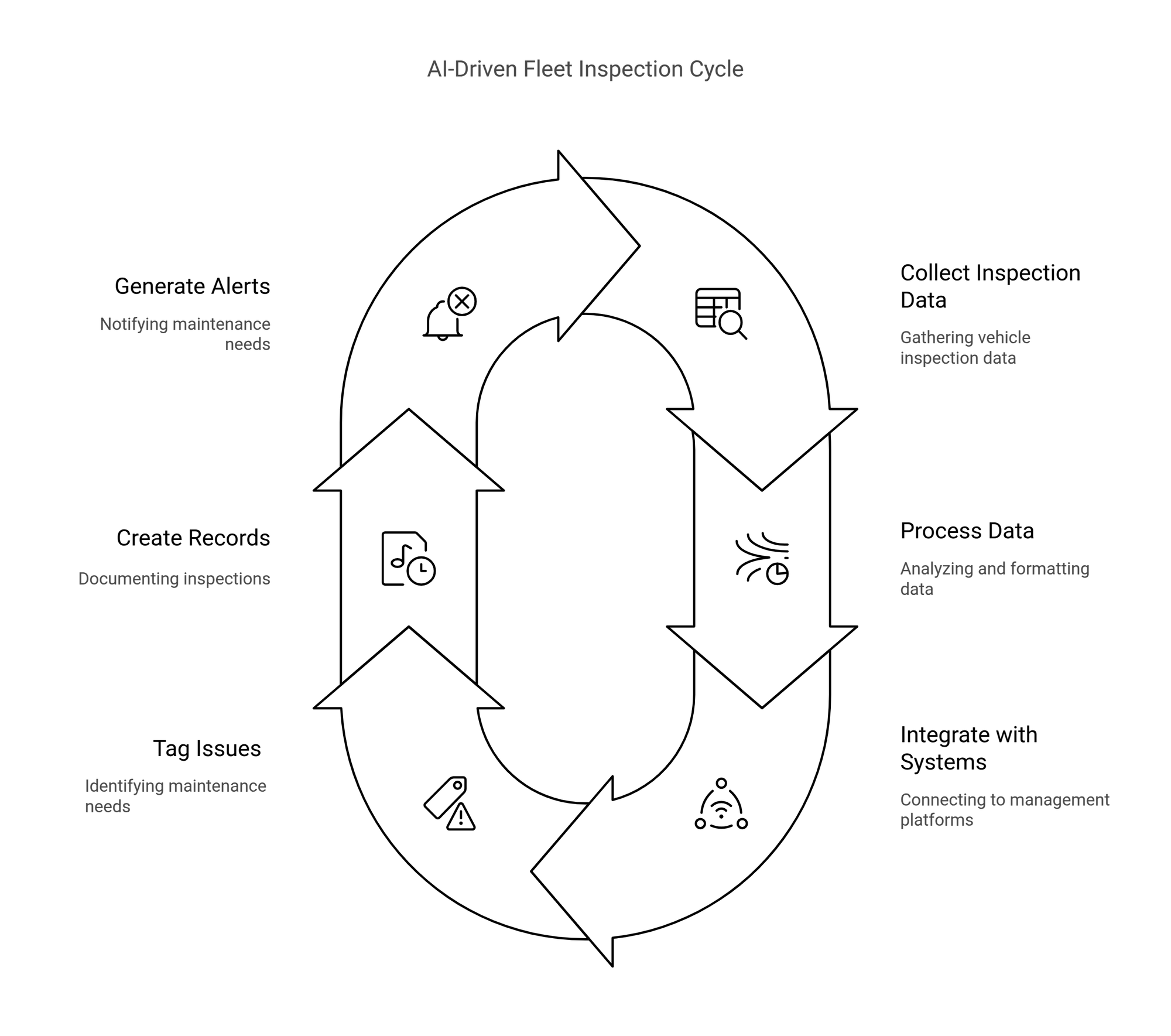
The AI doesn't just collect information. It processes inspection data and integrates it directly with fleet management systems. This capability:
Automatically formats responses into required documentation.
Integrates with existing maintenance management platforms.
Tags and categorizes potential maintenance issues.
Creates timestamped, verifiable inspection records.
Attaches photos or videos when necessary.
Generates maintenance alerts based on reported conditions.
Trucking companies have eliminated many hours of manual data entry after implementing AI inspection reporting, allowing maintenance coordinators to focus on addressing issues rather than processing paperwork.
Optimize Fleet Inspections with AI
Cut paperwork, boost compliance, and save driver time effortlessly.

Real-Time Compliance Verification
Perhaps the most valuable feature is the system's ability to ensure complete and compliant inspections before submission. The AI
Verifies all DOT-required inspection points are addressed.
Flags potentially serious safety issues for immediate attention.
Confirms inspection completeness before finalizing reports.
Adapts to changing regulations automatically.
Provides compliance verification documentation.
Ensures consistent inspection quality across the fleet.
Safety directors at passenger transport companies have noticed significant improvements during DOT audits after implementation. The system simply doesn't let inspections fall through the cracks.
Real Business Benefits for Transportation Operations
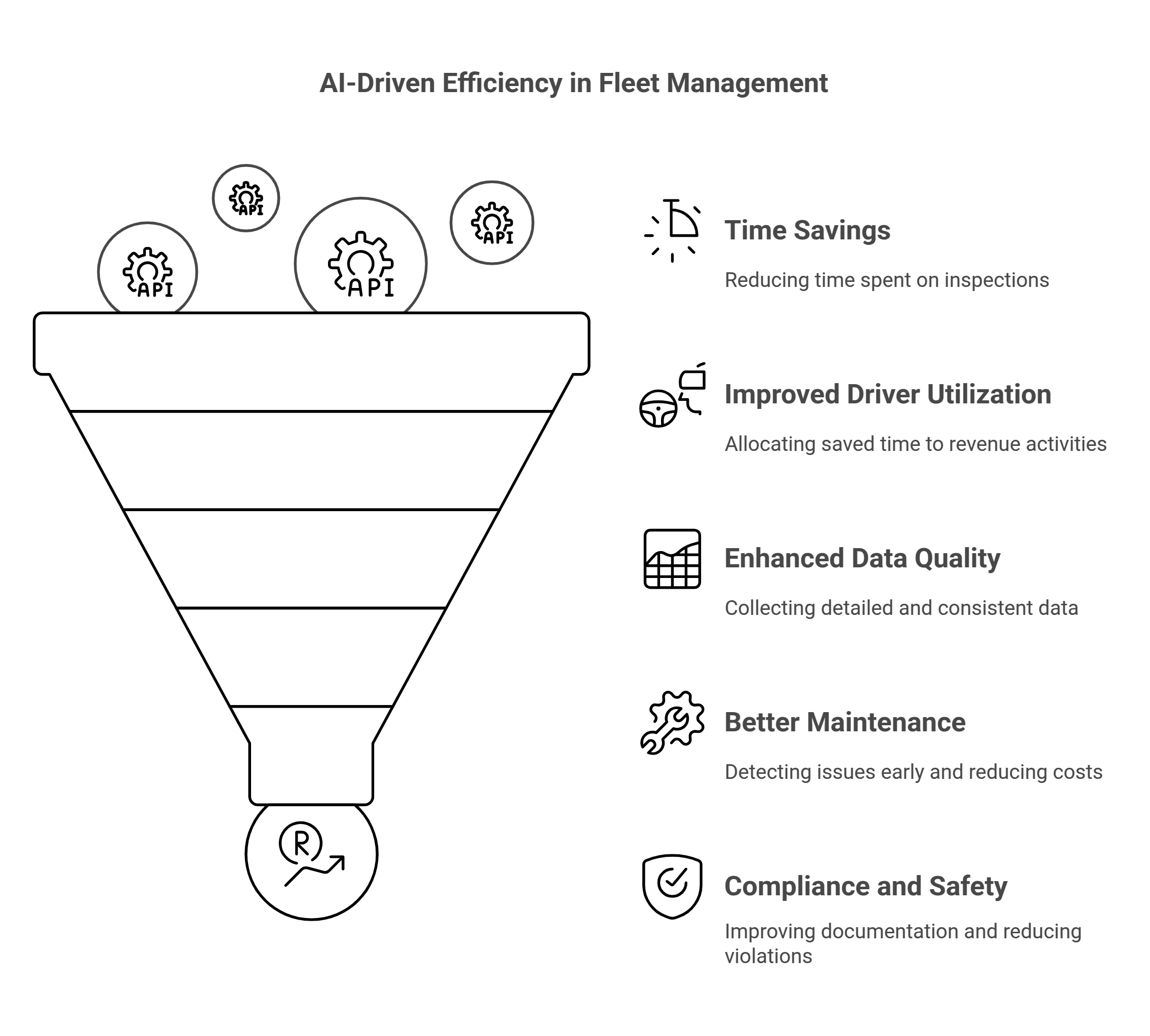
Operational Efficiency Through Streamlined Reporting
The most immediate impact comes from time savings. Companies implementing AI inspection reporting typically reduce driver inspection time substantially, translating to many minutes saved per driver daily.
For even modest-sized fleets, this efficiency represents thousands of hours annually that can be redirected to revenue-generating activities or improved driver rest periods.
Fleet operators have calculated significant savings in the first year through improved driver utilization alone.
As operations managers often note, in this industry, time is literally money. Getting drivers back on the road or to much-needed rest periods instead of doing paperwork makes a real difference to the bottom line.
Improved Maintenance Through Better Data Quality
The consistency and detail of AI-collected inspection data significantly improve maintenance operations. Companies report
Earlier detection of developing mechanical issues.
Reduction in roadside breakdowns.
Decrease in unplanned maintenance costs.
More effective parts inventory management.
Better tracking of recurring issues across vehicle models.
Improved communication between drivers and maintenance staff.
Transit operators have documented notable reductions in maintenance costs within months after implementation.
Maintenance teams report catching small problems before they become expensive repairs or safety issues due to improved information quality from drivers.
Improved Compliance and Safety Outcomes
For safety and compliance managers, the system delivers substantial risk reduction benefits.
Complete, consistent inspection documentation.
Immediate notification of safety-critical issues.
Clear audit trails for regulatory requirements.
Statistical analysis of inspection trends.
Reduced liability exposure through documentation quality.
Improved CSA scores through fewer violations.
Implementation Guidance for Transportation Companies
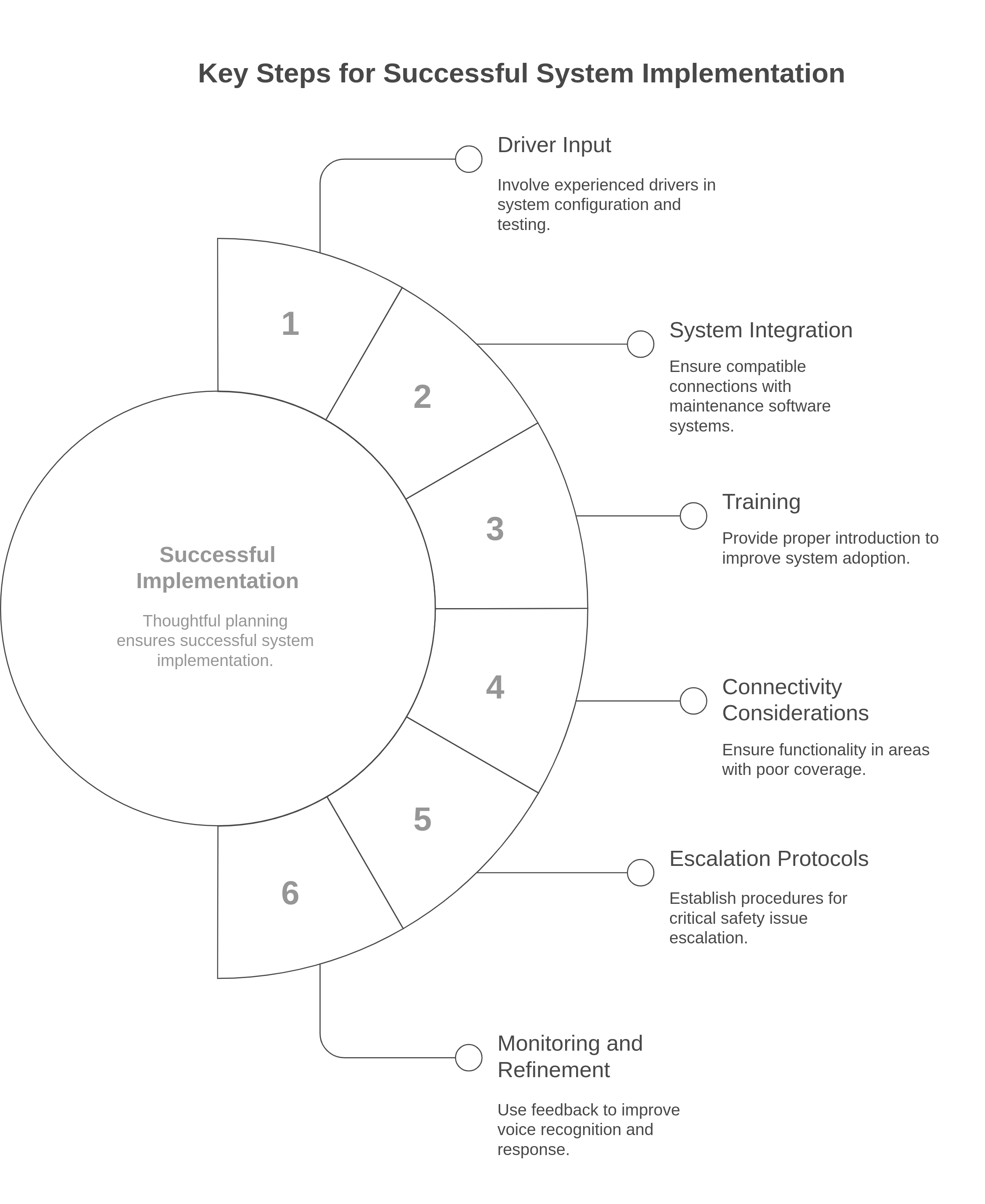
While the benefits are compelling, successful implementation requires thoughtful planning.
Start with driver input – involve experienced drivers in system configuration and testing.
Integrate with existing systems – ensure compatible connections with maintenance software.
Provide adequate training – despite the intuitive interface, a proper introduction improves adoption.
Consider connectivity limitations – ensure the system functions effectively in areas with poor coverage.
Develop clear escalation protocols – establish procedures for critical safety issues identified during inspections.
Monitor and refine – use early feedback to improve voice recognition and response patterns.
Regional carriers have found that short pilot programs with small driver groups provide valuable insights that improve eventual company-wide rollouts.
The time spent gathering driver feedback before full implementation pays off tremendously in adoption rates.
Transform Vehicle Inspections Today
Automate reporting and streamline compliance. Let’s talk!

The Future of AI in Vehicle Inspections
As these technologies mature, transportation companies can expect several promising developments:
Integration with telematics data to correlate operational patterns with inspection findings.
Computer vision capabilities to automatically detect visible defects.
Predictive analysis identifies potential failures before they occur.
Advanced diagnostics through integration with vehicle systems.
Augmented reality guidance for complex inspection procedures.
Multi-lingual support for diverse driver workforces.
Conclusion
AI-powered inspection reporting transforms what has traditionally been viewed as a necessary burden into a strategic advantage.
By making inspections more efficient, more accurate, and less frustrating for drivers, these systems deliver immediate operational benefits while enhancing safety and compliance.
For transportation companies seeking to optimize their operations while improving their safety profile, AI inspection agents offer a practical solution with demonstrable return on investment.
As regulatory requirements continue to evolve and driver time becomes increasingly valuable, these systems will become essential tools in competitive fleet operations.
Looking to integrate AI in your existing system? Contact us today!
FAQs
How long does implementation typically take?
Most fleets can implement AI inspection reporting in several weeks, including integration, testing, and driver training.
Does the system work for all commercial vehicle types?
Yes, the inspection protocols can be customized for everything from passenger vans to heavy trucks and specialized equipment.
How do drivers typically adapt to the new system?
Most drivers become comfortable with the system within several inspection cycles, with younger drivers typically adapting more quickly than veterans.
What happens when connectivity is limited?
The best systems operate offline and synchronize data when connectivity is restored, ensuring uninterrupted operations.
How does this affect roadside inspections by DOT officers?
Most companies report smoother roadside inspections due to more complete documentation and consistent inspection practices.